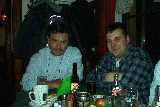 |
Hallo, wir
sind die beiden Mustang-infizierten Holzwürmer, links Günter und rechts
Dirk. Wir möchten je eine Ziroli-Mustang mit einer Spannweite von 248 cm
bauen. Wer sich dafür interessiert findet hier den Baubericht. Es wird
Schritt für Schritt vorangehen, aber das grobe Ziel ist auf zwei Jahre
Bauzeit gesteckt.Aber die nächsten zwei Jahre sind wir bestimmt mit den
Mustangs beschäftigt. |
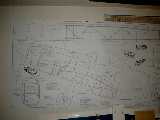 |
Das ist der
Rumpfplan von Nick Ziroli, eines von insgesamt 4 Blättern. Als wir uns
Plankopien zum zerstückeln fertigen lassen wollten, wussten wir auch,
weshalb der Plan so teuer ist. So ein Blatt kostet je nach Kopieranstalt
etwa 13-15 Euro. Da erscheint der Ziroli-Preis von 72 Euro für die 4 Blätter
fast geschenkt. |
 |
Der Einsatz
einer vernünftigen Dekupiersäge ist für ein solches Vorhaben unerlässlich,
viele Teile werden aus 3mm Pappel-Sperrholz gesägt. Die Platten kann man
mit einem Bürotacker paarweise zusammenheften, und gleich zwei Teile in
einem Arbeitsgang herstellen. Bei zwei Maschinen ist der Arbeitsaufwand
deutlich reduziert. Dann wird die Kopie des Planes mit einem Klebestift
auf das Holz gebracht. Unzählige DIN A3 Kopien haben wir benötigt. Diese
waren immer noch zu klein und mussten aneinander geklebt werden. |
|
Spannweite
248 cm
Abfluggewicht schätzungsweise 17 kg
Motorisierung ZDZ 80 mit Krumscheid Resonanzschalldämpfer
pneumatisches Einziehfahrwerk von Hawe
Holz bauweise mit Anbauteilen aus GFK (Motorhaube und Ölkühlerhutze)
|
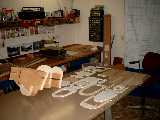 |
Die
Rumpfspanten aus Pappelsperrholz und eine fertig verleimte Motorbox. Die
Motorbox wird aus Gründen der Vibrationsfestigkeit aus
Buchenflugzeugsperrholz gefertigt. |
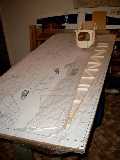 |
Die gesamte
Rumpfkonstruktion richtet sich auf dieser Hartbalsa-Verkastung aus. Alle
Rumpfspanten werden hier später "aufgefädelt". Daneben liegt
die bereits fertig verklebte Motorbox. |
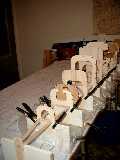 |
Dieser
Balsaholm ist wie eine durchgehende Richtschnur, der Rumpf kann so auf
einer Helling gebaut werden, die aus Spanplattenwinkeln besteht. Die
Mittellinie auf dem Winkel nach oben übertragen, so können die
Rumpfspanten rechtwinklig und gleichzeitig mittig verleimt werden. |
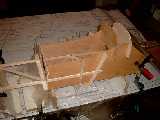 |
Verleimen
der Motorbox mit dem Rumpfholm. Vorsicht, noch wird alles nur vom
Balsaholm gehalten. |
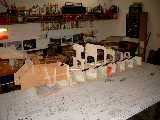 |
Alles schön
winklig ausrichten, der Plan ist von Hand gezeichnet, die Aussparungen
für die Leisten sind nicht ganz sauber aufgeteilt. Wenn die Spanten
gedreht werden, kann ein Verzug in den Leisten erfolgen. Darauf achten,
dass die Spanten alle aus Plandraufsicht in einer Richtung
ausgerichtet werden. |
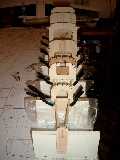 |
Der Spant für
die Befestigung des Heckfahrwerks wird wieder aus besonders hartem
Buchensperrholz gefertigt. |
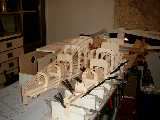 |
Leisten auf
der Unterseite |
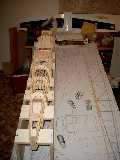 |
Hier sieht
man wie die komplette Rumpfkonstruktion nach dem Drehen wieder auf der
Holmverkastung abgestützt wird. Wir haben rechts und links eine
Spanplatte gestellt, und den Rumpf auf Querbrettchen abgelegt. Dabei wird
vor dem Einleimen der Leisten wieder die Mittellinie übertragen. Verzug
unmöglich ! |
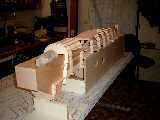 |
Hier seht
ihr schon den Sitz des Tanks und des Cockpits. |
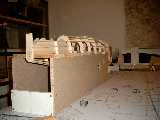 |
Hier ist die
Auflage für das Höhenleitwerk zu sehen. Der Plan sieht ein
durchgehendes, festeingebautes HLW vor. |
 |
Der
Resorohrtunnel wird auf einem Stück Regenrinne in GFK gefertigt. Unser
erster brauchbarer Kontakt mit Glasfasertechnik. Na , hat ja geklappt. |
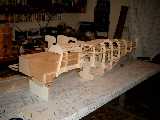 |
Der Rumpf
wird von der Helling genommen. Jetzt sollte er schon verwindungssteif
sein. |
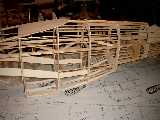 |
An der Ölkühlerhutze
ist das Teil ganz schön dick.... |
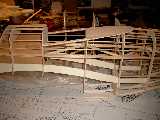 |
Sitz der
Tragfläche, die Ölkühlerpartie wird später abgetrennt und unter der
Tragfläche befestigt. Den Lufteinlass übernimmt ein vorgefertigtes
GFK-Teil. |
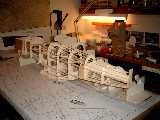 |
Langsam
sieht man was es mal werden soll..... |
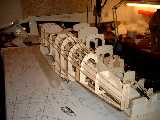 |
Bevor die
letzten Leisten eingeleimt werden, wird der Resorohrtunnel eingebaut. |
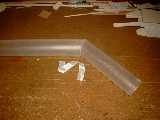 |
Der
Resotunnel soll in der Abluftklappe der Ölkühlerhutze enden. Dazu wird
er auf Gehrung geschnitten und mit einem GFK-Streifen verbunden. |
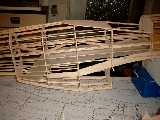 |
Der
GFK-Streifen muss in der Rumpfkonstruktion aufgebracht werden. Das Rohr
kann mit dem Knick nicht eingeschoben werden. Danach werden die restlichen
Leisten eingeleimt. Dabei passt der Rumpf auf keine Helling mehr. |
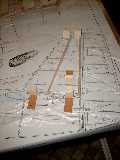 |
Montage des
Seitenleitwerks. Unter den Holm und die Endleiste kommen keilförmige
Leisten.Durch diese und die Stützwinkel können die Rippen rechtwinklig
eingeleimt werden. |
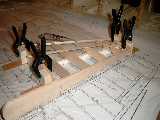 |
Alles im
Lot... |
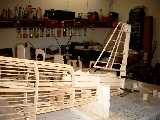 |
An der
Stelle wird es später angeleimt. |
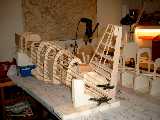 |
Vorher wird
das Höhenleitwerk benötigt. Wir überlegen noch, das Leitwerk mit
Steckung zu bauen, damit ist der Rumpf leichter beim Transport zu
handhaben. |
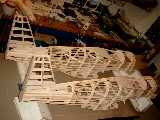 |
Die
beiden Rumpfrohbaugerüste. |
|
Letztes
Update Februar 2003 |